12 inch angle grinder RP-AG-20001
12 inch Angle Grinder is commonly used which is disc diamter 304.8mm. RP-AG-20001 Wheel Diameter Φ180/230MM, can also OEM and customize your size and brand.
Common models of Angle grinding machines are divided into 100 mm (4 inches), 125 mm (5 inches), 150 mm (6 inches), 180 mm (7 inches) and 230 mm (9 inches) according to the specifications of the accessories used, and the small-size Angle grinding machines used in Europe and the United States are 115 mm.
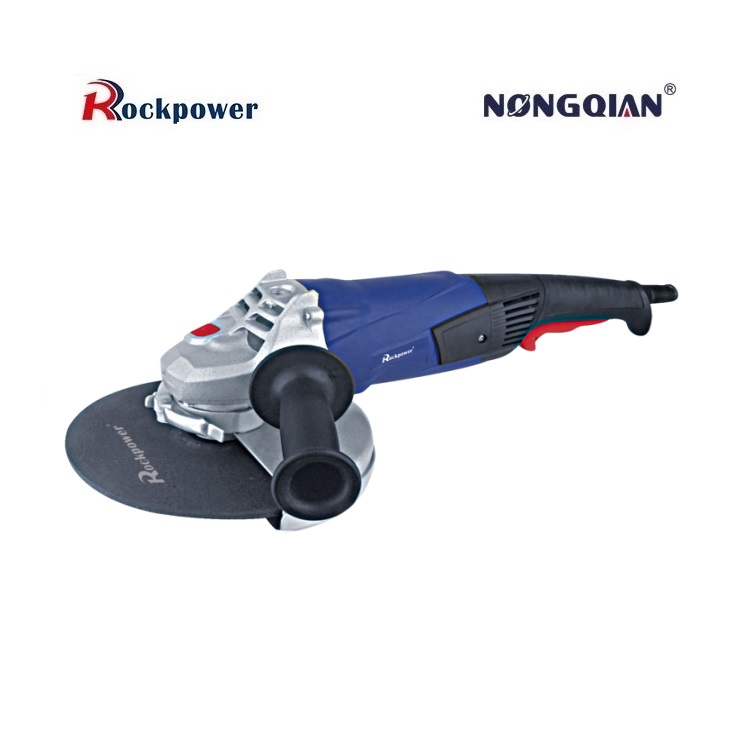
Angle Grinder RP-AG-20001
Item Name | Parameters |
Rated Voltage | 110/220V |
Rated Frequency | 50/60Hz |
Max Wheel Diameter | Φ180/230MM |
Hole Diameter of Wheel | Φ16mm |
Rated Input Power | 2000/2200W |
No-Load Speed | 6500r/min |
Related Products:
Click here to see more Video
Product Details
Descriptions about Angle Grinder
Exhibition Pictures
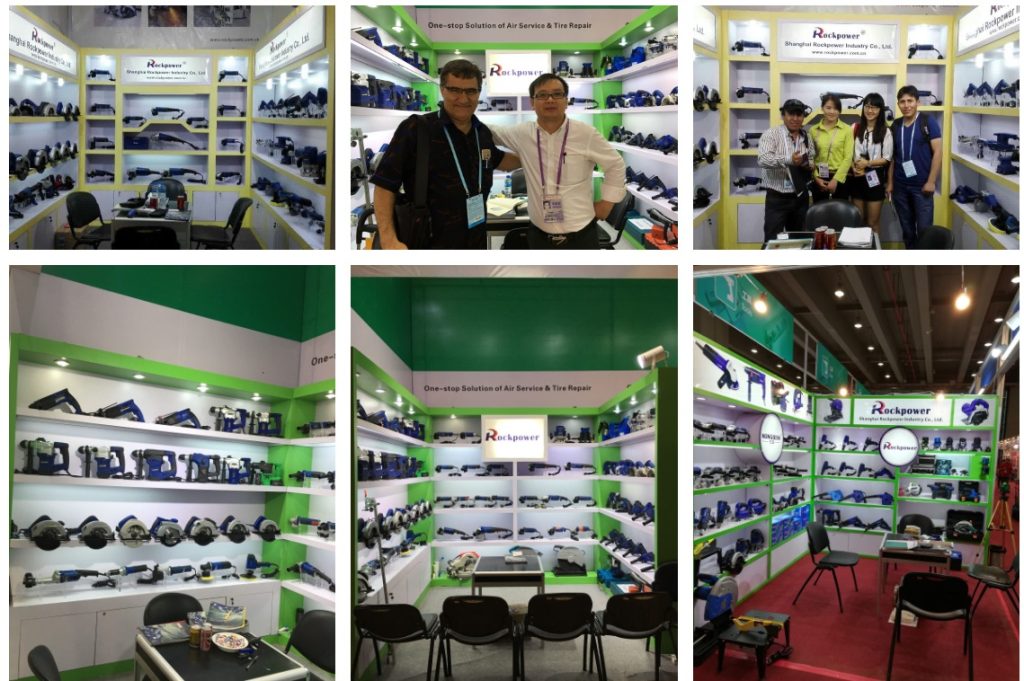
The goods are packed according to customer special requirement. The shipping is fast and safe.
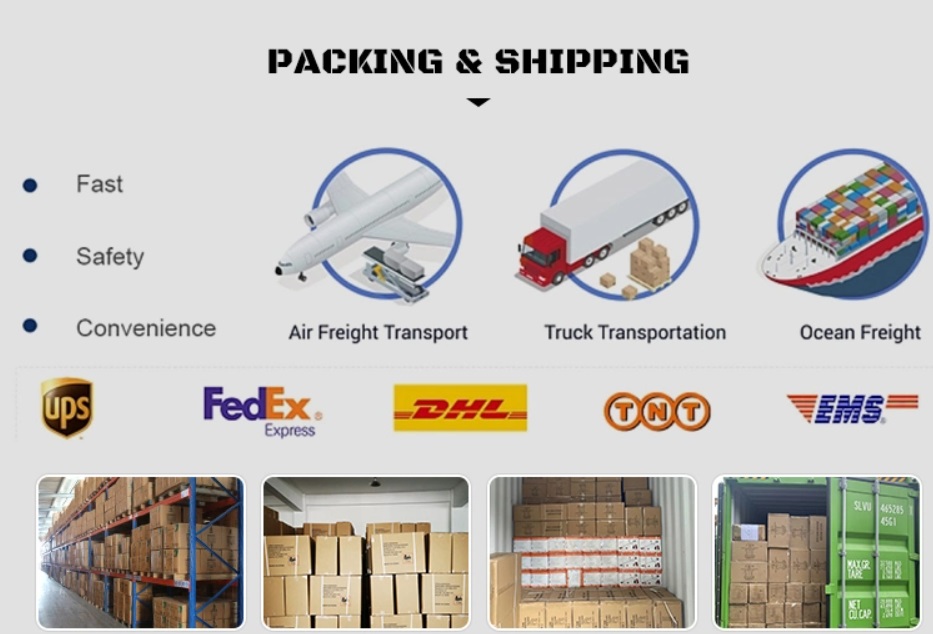
Factory Warehouse
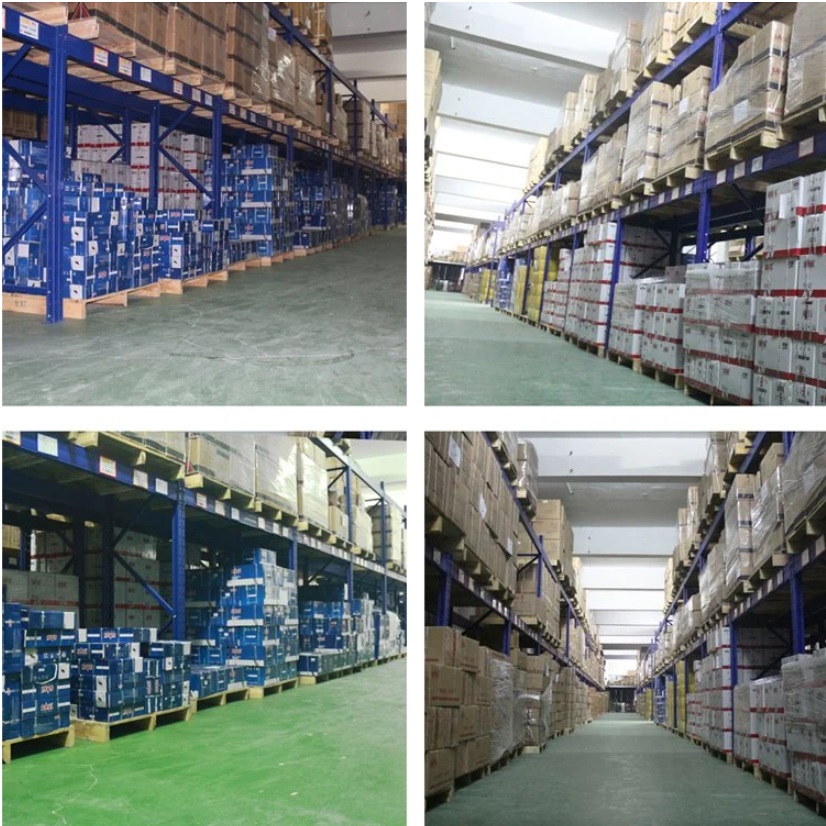
This is the process flow chart and OEM process flow chart. For details please contact with our sales.
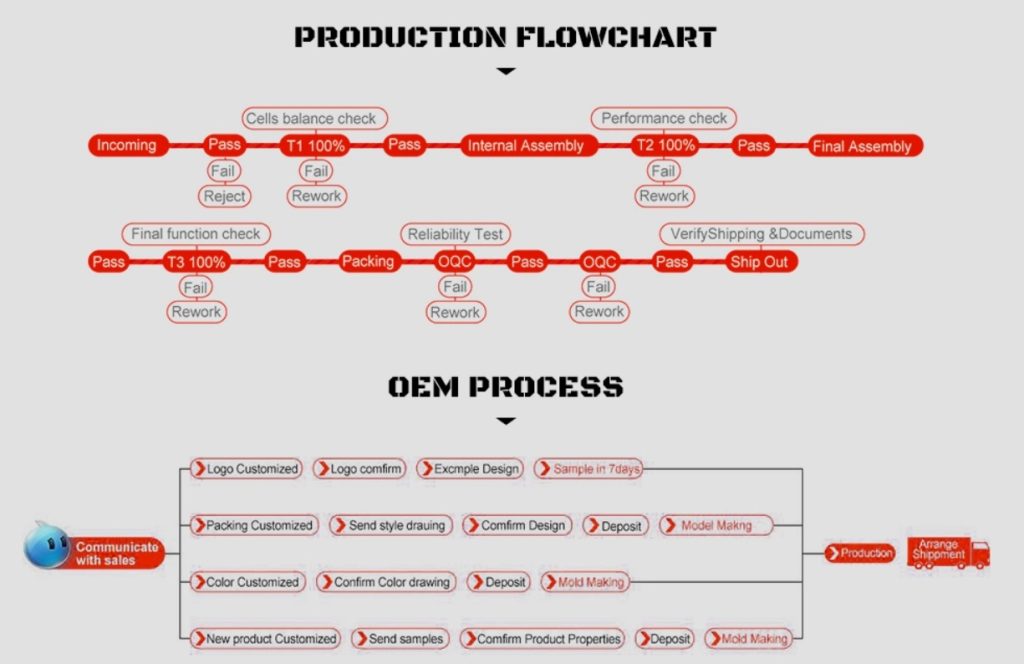
Safety warnings specifically for grinding and abrasive cutting operations
a) Use only the type of wheel recommended for power tools and the specific guard designed for the selected wheel. Wheels for which power tools are not designed cannot be adequately protected and are unsafe.
b) The grinding surface of the concave wheel must be installed below the lip guard plane. Improperly mounted wheels protruding through the protective lip plane cannot be adequately protected.
c) The guard must be securely attached to the power tool and must be positioned to ensure maximum safety so that the minimum amount of wheel is exposed to the operator. The guard helps protect the operator from broken wheel debris, accidental contact with the wheel, and sparks that can ignite clothing.
d) Wheels should only be used for recommended applications. Ex ample: Do not grind with the side of the cutting wheel. Abrasive cutting wheels are used for peripheral grinding, and the lateral forces applied to these wheels can cause them to break.
e) Always use undamaged wheel flanges with the correct size and shape of the selected wheel. The correct wheel flange supports the wheel, thus reducing the possibility of wheel breakage. The flange of the cutoff wheel may differ from that of the grinding wheel.
f) Do not use large power tools worn wheels. Grinding wheels for larger power tools are not suitable for the higher speeds of smaller tools and may burst.
Additional safety warnings for abrasive cutting operations
a) Do not “jam” the cutting wheel or apply excessive pressure. Do not attempt to cut too deep. Applying too much stress to the wheel increases the load and the susceptibility of the wheel to twisting or binding at the cut, and increases the likelihood of recoil or wheel breakage.
b) Do not align your body with and behind the rotating wheel. When the wheel leaves the body at the operating point, the possible recoil may push the spinning wheel and power tools directly towards you.
c) When the wheel is bound or the cutting is interrupted for any reason, turn off the power tool and keep the power tool still until the wheel is completely stopped. Do not attempt to remove the cutting wheel from the cut while the grinding wheel is in motion, or a recoil may occur. Investigate and take corrective action to eliminate the cause of wheel adhesion.
d) Do not restart the cutting operation on the workpiece. Allow the grinding wheel to reach full speed, then carefully re-enter the cut. If the power tool restarts in the workpiece, the grinding wheel may bind, walk, or recoil.
e) Support plates or any over-sized workpiece to minimize the risk of wheel extrusion and recoil. Large workpieces tend to sag under their own weight. Supports must be placed near the cutting line and near the edge of the workpiece on both sides of the grinding wheel.
f) Use extreme caution when making “pocket cuts” to existing walls or other blind areas. Protruding wheels may cut gas or water pipes, electrical wires or objects that may cause recoil.
FAQ
Pleas contact with us if you can not find your answer in FAQs.